Situated in south-east England, the Port of Dover enables the movement of people and the exchange of trade, and is Europe’s busiest international ferry ports. It handles 33 per cent of all trade with the European Union and is a key gateway for international tourists, handling 1.3 million tourist vehicles and over 6 million passengers every year. The Port’s estate is divided into the Eastern and Western Docks, which include a purpose-built cargo terminal and marina curve with more than 60 buildings spread across the Docks. Owned by the Dover Harbour Board, the Port has a rich history and is home to a number of listed buildings and structures.
About the partnership
We initially won the Port of Dover contract in 2016. The contract evolved over time with the team making improvements and supporting the client through a number of major events, including Brexit and the pandemic and even getting to grips with the natural environment at the Port as well.
The services we provide to the Port have varied over the years, but currently include the following:
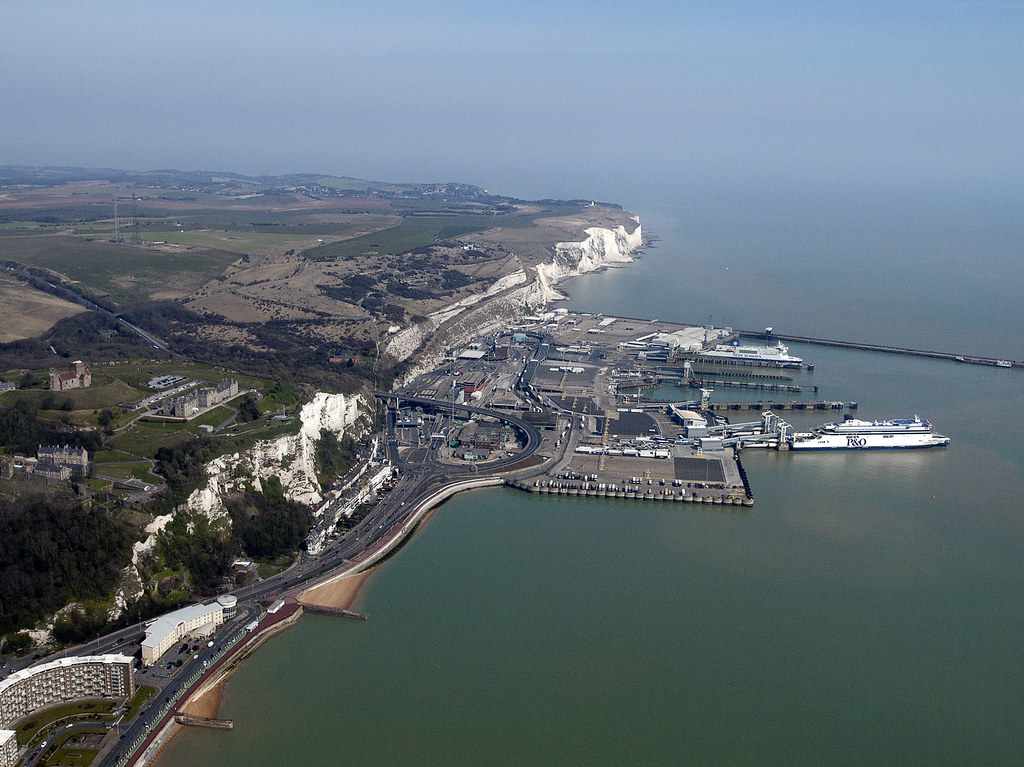
- Cleaning of the cruise terminals
- Cleaning of cargo welfare and storage facility – cargo walls and shutters are cleaned by hand by a specialist team
- Cleaning of office and admin buildings
- Cleaning of marina buildings
- Cleaning of passenger welfare buildings, including toilets, food area, showers, receptions, berths and berth portals, as well as multi-purpose check-in booths
- Daily mechanical sweep of piers to remove guano to allow tug staff to work safely
- Road sweeping
- Litter picking
- Gully cleaning
- Beach cleaning
- Jet washing
- Window cleaning
- Washroom services
- Consumables
- Carpet cleaning
- Landscaping
- Cover for events such as the Regatta, Marina Day and cruise events
We work to an output specification with buildings graded as gold (high traffic and public areas), silver (office accommodation) or bronze (non-accessed areas) depending on their importance.
The cleaning is very seasonal – the first two and last two weeks of summer are particularly busy at the Port with people going and returning from holiday, as well as the Christmas period when stock gets delivered to the UK. We increase cover and adjust our schedules to support the client during these busy times. January and February are usually less busy which is when we tend to carry out some of the deep cleans to ensure minimal disruption.
We are very accommodating and flexible when it comes to providing our services at times that suit the client, which has been key to maintaining a successful partnership over the years. Due to the constant stream of traffic, access to some areas for pressure washing and window cleaning has to be planned in advance with the client to fit around road closures and seasonal traffic.
Making our mark
After winning the customer, we quickly got to work, as there were a number of changes needed to ensure an efficient service delivery on this busy contract.
Firstly, we introduced a management structure which included a dedicated site manager to oversee and support the team on the ground. We then carried out detailed time and motion studies across the whole site to create route plans and grid schedules. Following on from this, we provided each team member with a detailed list of tasks they need to complete when assigned an area, so that everyone knew what they were doing and how much time was needed to complete a task. These changes were well received by the team and the client and had a significant contribution to the improvement of team morale and cleaning standards across the Port.
We implemented our digital platform Mo:dus to host a number of key functionalities and improvements we were making. Mo:dus allows us to monitor contract performance and the client has full visibility via the client portal. The platform provides the basis of detailed plans for optimising and ensuring all schedules of work are planned for. We also launched a helpdesk function to enable the logging and categorising of service calls and instant allocation of jobs. The helpdesk is co-ordinated by a dedicated on-site administrator who works in real time with Mo:dus. Additionally, via the system we instigated schedules for Planned Preventative Maintenance (PPM) delivery and made sure that all works were completed on time and to required standard, which has in turn reduced the number of reactive calls to the helpdesk. Furthermore, we introduced auditing via Mo:dus to provide accountability across all sites.
All of these improvements laid a strong foundation for a consistent service delivery at the Port.
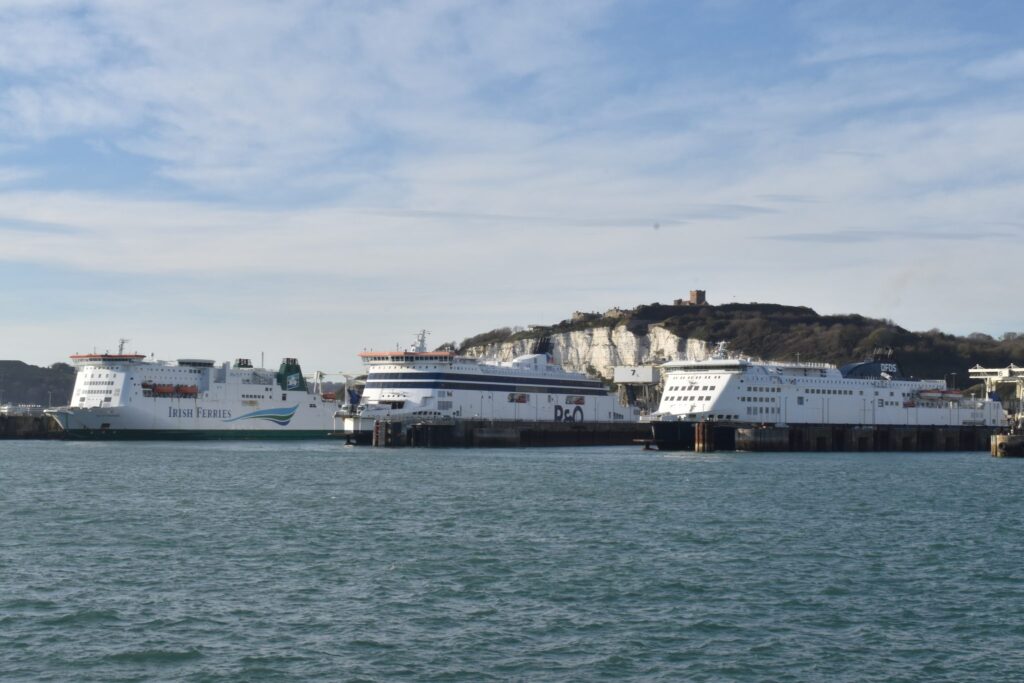
Making time for nature
A year into the initial contract, landscaping was added to our remit. The main concentration was to bring the areas up to a maintainable condition by cutting back trees, hedges and weeding accessible areas.
We brought in a dedicated landscape gardener, which allowed us to conduct a full review of all gardening areas from seafront to planters and beds, as well as assess the suitability of the plants and shrubs on the estate. Prior to us taking over, bedding plants were put in every single year at the Port.
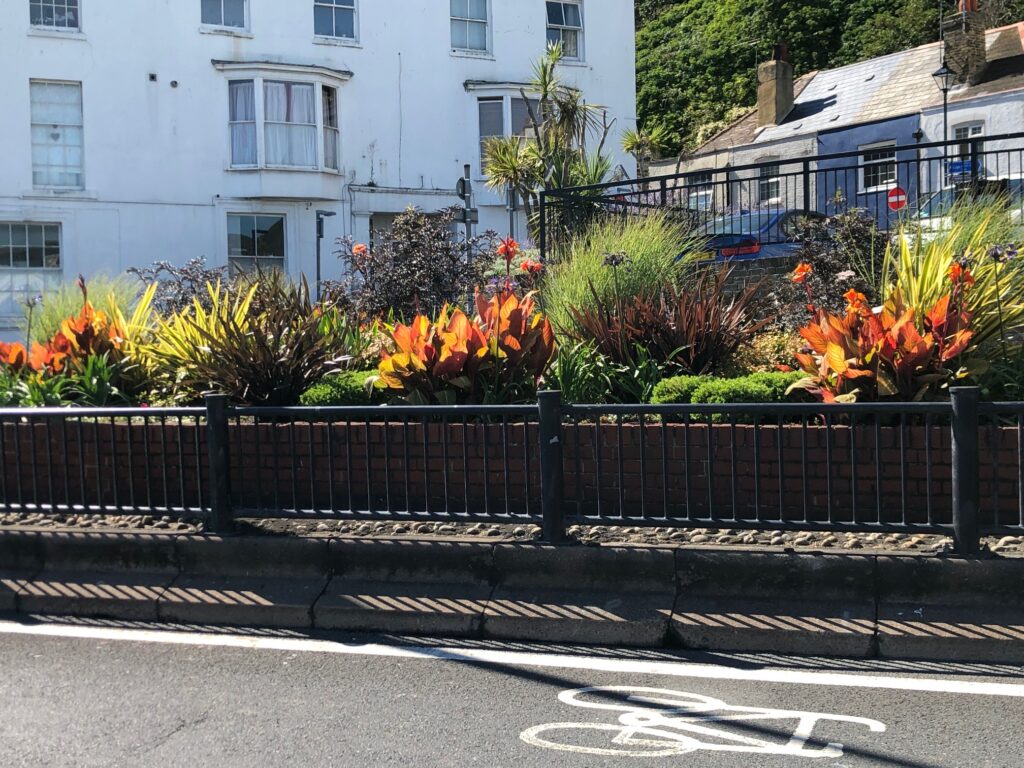
Our specification for the garden proposed the implementation of perennial plants which live longer than one season. It also offered thoroughly researched plant recommendations that would thrive in the seafaring environment which closely matched the plants that were originally put in over 100 years ago. A lot of thought has gone into this, considering the maintenance and the design as to what placement of plants and colour ranges would look the best.
The move away from annual bedding plants resulted in substantial savings for the client, offering a more sustainable and financially viable solution going forward. Once the perennial plants have bed in, they have enhanced the front of the Port and the seafront appearance, and we regularly receive compliments from the residents as to how it looks.
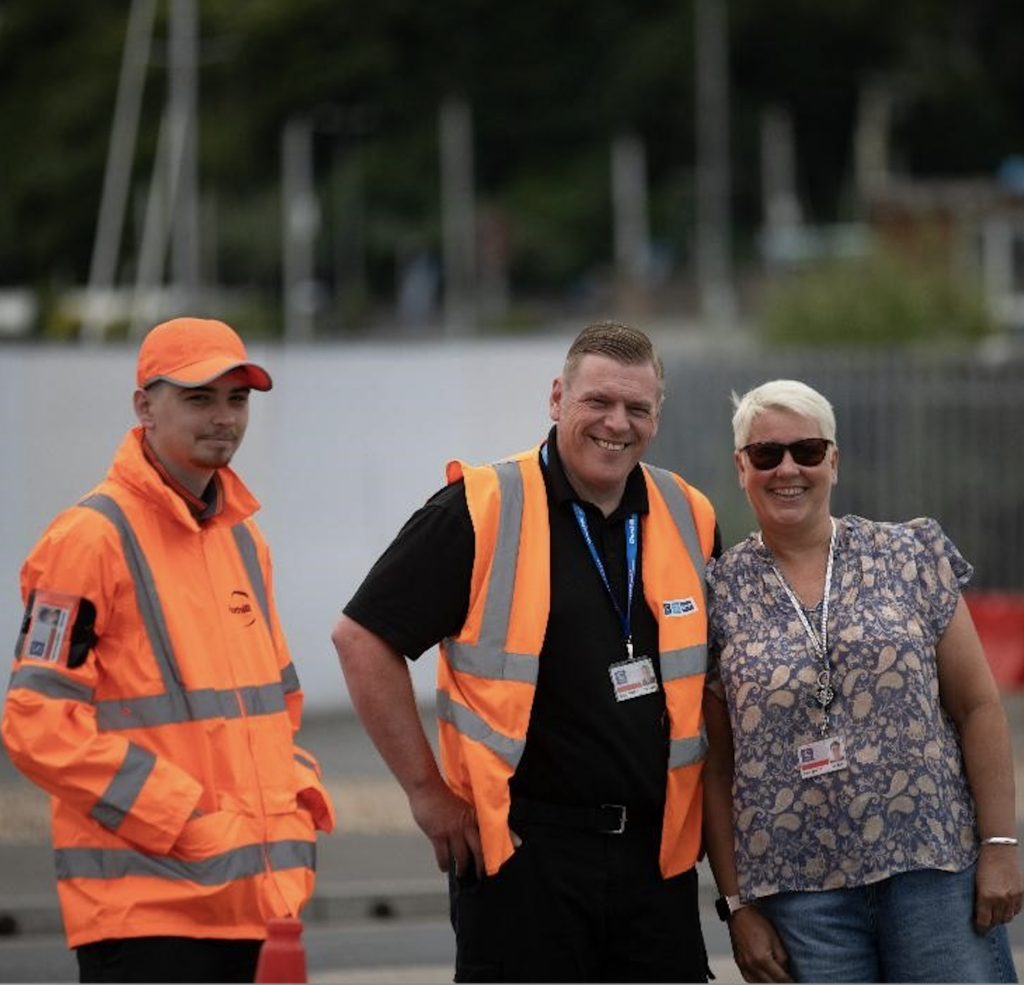
A dedicated team that drives efficiencies at the Port
The contract is led by Contract Manager Tracy Bear. Tracy has developed a great partnership with the client over the years and is supported by a business support manager, night support manager, five supervisors and a specialist cleaning team that are all doing a fantastic job ensuring a consistent service delivery since day one.
52 Churchill colleagues work at this critical national infrastructure site 24/7, 364 days a year (the Port only closes on Christmas day) with even split of day shift and night shift patterns.
The team works in an always busy environment, and the Port takes safety and security very seriously. All team members must undergo the Port’s GSSAT security and safety training, as well as Action Counters Terrorism training. There is a strict vetting process in place for everyone working at the Port, with all Churchill team members required to have a basic DBS check with additional Port checks before they can be issued a pass.
Effective communication on this large site is essential for team safety and efficient service. The team is issued with mobile phones and teams on night shifts also have panic alarms and work in pairs for safety. There are seven vehicles used by the team to get around the site including a Hilux vehicle, Scarab sweeper and five vans.
We regularly upskill our team to improve performance and deliver efficiencies for the client. We conduct management and supervisor training, e-learning, one to one training sessions for operatives, toolbox talks, as well as provide specialist training for specific jobs around the Port, such as sweeper training, weed control spray training, gardening training and IPAF training.
At our annual Shining Stars event in 2024, the Port of Dover team won the Dream Team award. You can meet the team and learn a little more about why:
Sustainability at the Port
We work closely with the client and our suppliers to deliver a broad spectrum of sustainable best practices across the contract, some of which are listed below:
- Purex, a chemical-free cleaning solution, whereby water passes through seven stages of unique micro-filtration, is used across the Port.
- We implemented our PVA sustainable cleaning range by replacing plastic containers with PVA water soluble cleaning sachets. This has not only delivered a plastic saving of 540kg in a single year, but has also significantly reduced our carbon emissions, as the PVA range is more sustainable for storage and transport.
- Hand driers across the Port were replaced with phs energy efficient hand driers which has generated energy savings for the client.
- As mentioned earlier in this case study, we provided a more sustainable and cost-effective gardening solution by replacing the bedding plants with perennials which endure year around and do not have to be replaced each year.
- We transferred all paper consumables supplied to the Port to Metsä paper products. Metsä is our preferred provider of paper products and a renowned leader in sustainable forestry.
- All Churchill colleagues working on this contract are paid according to the Living Wage Foundation, which is greater than the National Living Wage to ensure that employees are paid in accordance with the real cost of living and can live comfortably on their earnings.
A flexible partner that adapts
We became a trusted partner to the Port of Dover and on a number of occasions demonstrated our commitment and ability to ensure service continuity and flexibility during challenging times.
We produced and followed bespoke business continuity plans for Brexit and the pandemic which outlined the supply of resources and services in the event of the Port getting blocked, and specified the storage and provision of consumables to ensure sufficient supply.
Over the years, we also supported the client through protests, strikes and storms which cause regular delays and often gridlock Dover. During these times, we adapt our schedules to ensure all busy public areas are covered and facilitate staff transportation to site, as well as double up or reroute the deliveries of consumables.
We are very flexible in our approach and always find a solution to support the client, no matter the requirement. For example, we previously supplied milk to the Port, took on the management of boiler servicing for a period of time and upskilled members of the team to deal with plumbing incidents whilst the client was having supplier challenges.
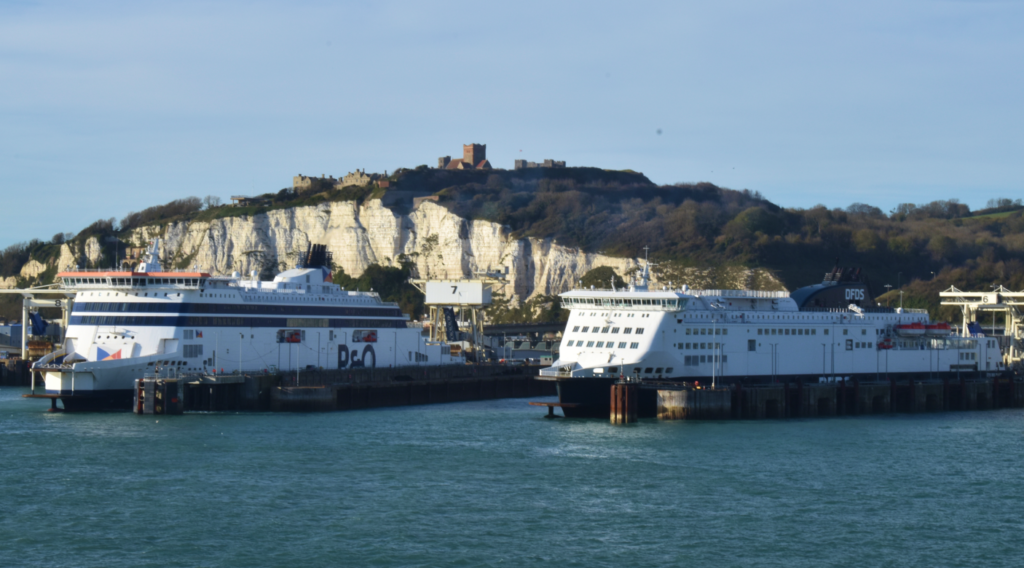
The results
Since introducing our helpdesk function, we have recorded a continued reduction in reactive calls which can be attributed to a number of factors, including regular assessment and adjustment of our working schedules and frequencies, flexibility of our service delivery, collaborative partnership between the Churchill team and other on-site teams, as well as increased completion of PPM works. Our quality audits consistently score above the 85% target and the compliments received via the customer survey significantly outweigh the complaints (in 2023 we received 84 compliments and 3 complaints which were rectified within 24 hours).
We have successfully addressed challenges inherited from the previous supplier and are working closely with the Port of Dover to ensure the cleaning contract is an ongoing success.